Uncover the Hidden Barriers to Your Success Today
The 6th breakdown, yet we are not close to end month, it’s no longer a minor inconvenience. It is slowing your operations, and you are losing business opportunities.
Every time a machine goes down, it affects your production, revenue, and customer satisfaction. If your organization is struggling to meet customer demands due to machine downtime, it’s time to take action.
The Profitability Challenge
Machine maintenance is often neglected until it’s too late, but the cost of downtime is staggering.
One of your machine has now broken down for the sixth time in October. Each breakdown leads to four hours of lost production, which could have otherwise produced 500 units. With each unit generating $50 in revenue, your business is losing $25,000 each time the machine stops working. That’s $150,000 of lost revenue in one month—all because of poor machine maintenance.
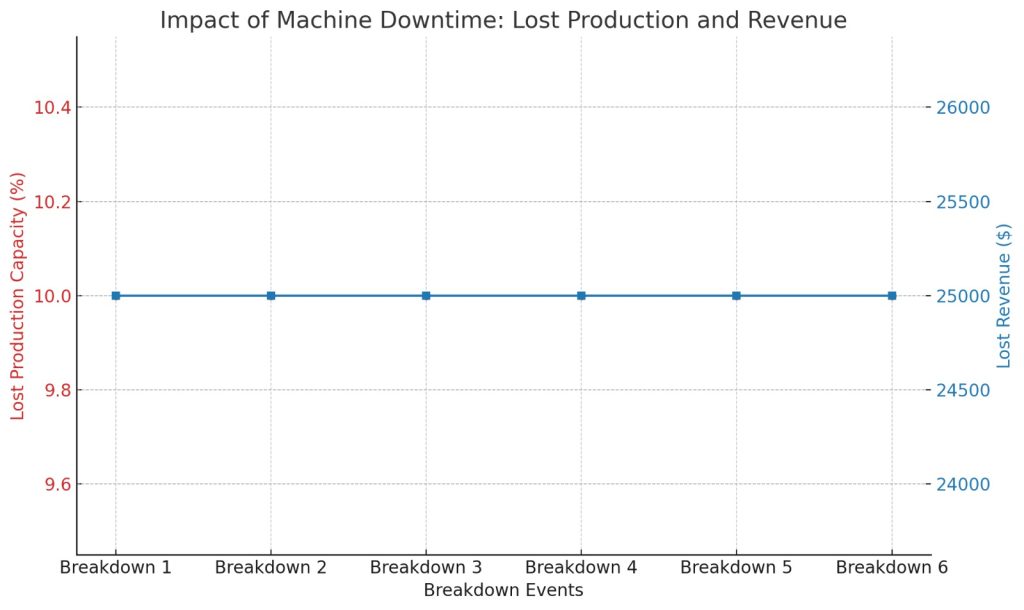
Now, what if those lost units were supposed to fulfill a major customer order?
You have not only lose revenue, but you might also lose the customer entirely due to unmet deadlines. Machine downtime directly impacts your ability to serve customers and maintain profitability.
Downtime and Production Rate:
Each time breakdown happens, and an organization records a loss of 10% for example of their daily production capacity, it will result in missed orders and unsatisfied customers. Over time, their reputation suffered, and competitors took advantage of the gaps they left in the market.
This case is a wake-up call for any business owner who thinks machine downtime is just another part of business operations. It’s not, it’s a threat to your growth.
The Solution
If your machines are costing you money and opportunities, how do you address this?
Implement Kaizen—a continuous improvement process that focuses on identifying inefficiencies and resolving them at the root cause.
Kaizen can help you analyze and streamline your operations, improving machine maintenance and reducing downtime. By applying Kaizen, businesses are able to:
• Increase equipment reliability
• Implement preventive maintenance schedules
• Involve employees in identifying issues early
• Improve operational flow and reduce delays
• Enhance customer service by meeting deadlines consistently
Key Questions to Ask
• How often are machines breaking down?
• What is the financial cost of these breakdowns?
• How are these breakdowns affecting customer satisfaction?
• Are we maintaining a proactive maintenance schedule, or are we waiting until machines fail?
• How can we improve our operational flow to reduce the impact of downtime?
Asking these questions, you will have a clearer understanding of the underlying issues in your operations and how to address them.
Saving Your Operations
To safeguard your business from machine downtime, adopt a preventive maintenance mindset, prioritize your operations, and embrace Kaizen practices. It’s not enough to react when things go wrong; you must actively prevent these issues from occurring. Kaizen helps reduce downtime and also improves overall production efficiency and enhances customer satisfaction.
Conclusion
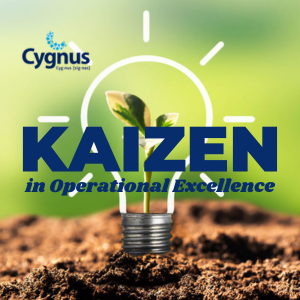
Don’t let machine downtime cripple your business. Take proactive steps by implementing a maintenance strategy and adopting Kaizen to ensure that your operations are not just meeting but exceeding customer expectations. When machines run smoothly, your business can do the same, driving profitability and growth.