Managing Sharp Edges In Work At Height Operations
Safety is the cornerstone of every successful operation in telecommunications and work-at-height projects. These environments present unique risks that must be managed and one of the most overlooked dangers is the presence of sharp edges that can compromise safety equipment, particularly ropes.
The Hidden Dangers of Sharp Edges
Despite advancements in rope technology making them almost unbreakable under normal conditions, sharp edges can still pose severe risks. Slight movements of a fully loaded rope against a sharp edge can lead to wear and even catastrophic failure. This is a risk that many work-at-height professionals face daily, and managing these hazards requires vigilance.
As a general guideline, any edge with a radius of less than 5 mm should be regarded as potentially hazardous, especially to soft materials like ropes and slings.
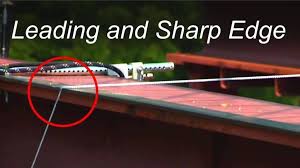
These edges, whether found on building facades, equipment, or natural environments, can degrade the integrity of your rigging system. Therefore, implementing the right safety practices is recommended and essential for long-lasting operations.
Strategies to Manage Sharp Edges
To protect yourself and your team, it is crucial to adopt the best strategies for managing sharp edges during rigging operations. Below is a hierarchy of controls, listed from the most effective to the least, that can be incorporated into your safety protocols:
- Avoid the Edge. The most straightforward and effective solution is to avoid sharp edges entirely. This may involve repositioning your rigging system or using tools like davit arms or Building Maintenance Units (BMUs) that extend the anchor point beyond the edge. For rope access technicians, techniques such as deviations, re-belays, or Y-hangs can be employed to keep ropes clear of dangerous edges.
- Modify the Edge. If it’s not possible to avoid the edge, consider modifying it. With permission from the building or project owner, you can smooth or round sharp edges using grinders or files. This reduces the risk to your ropes and also enhances the overall safety of the operation.
- Use Edge Protection. Edge protection is one of the most commonly used methods to manage sharp edges. However, not all protection is created equal. Soft edge protection is useful for minor abrasions but may fail under heavy loads or in high-friction scenarios. In more demanding environments, hard edge protection, like cargo corners or steel pipes, should be considered. Specialized ropes with built-in edge resistance, such as the Gravity Gear Shock Absorbing Lanyard, can also provide added security.
- Do Not Proceed if Risks Cannot Be Mitigated. Sometimes, none of these methods may be feasible or effective enough to mitigate risks. In such cases, the safest option is to halt the operation. No job is worth risking the life of your team or compromising the equipment.
Proactive Measures for Rigging Operations
Rigging operations are dynamic, with ropes moving constantly over various surfaces, which increases wear and tear. One effective way to reduce friction and enhance safety is to use edge rollers, allowing ropes to glide smoothly over sharp edges. This minimizes chafing and extends the lifespan of your equipment, ensuring safer and more efficient lifting operations.
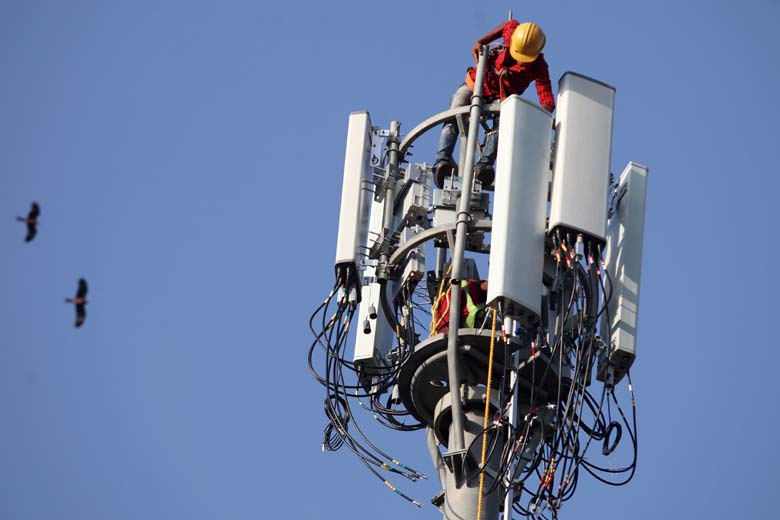
Be Proactive, Stay Safe
Safety in height work is about being proactive and prepared. By understanding the risks of sharp edges and using the appropriate protective measures, riggers, safety managers, and work-at-height personnel can prevent accidents and maintain their equipment for long-lasting operations.
Remember, safety is an ongoing commitment, and it starts with you.
For further guidance on managing sharp edges and improving your safety protocols, don’t hesitate to contact professionals who specialize in work-at-height safety training. Stay safe, stay prepared!
Read More Content From Our Blogs
Building for the Future: Why Safety & Operational Excellence Matter
Building for the Future: Why Safety & Operational Excellence Matter In the construction industry, every decision impacts the future of the project and that of the people working on it. Sustainability is about the systems, processes, and safety measures that keep projects efficient, profitable, and future-proof. Why Safety & Operational Excellence Matter in Construction Sites…
Sustainable Construction: Turning Efficiency into Profitability
When your construction project is on schedule and under budget, clients will rave about your eco-friendly approach, you will think it’s an ideal scena
Construction Site Risks and Hazards
Risk assessment is the foundation of a safe construction site. But what does it entail? Risk assessment involves identifying potential hazards, evaluating the risks associated with those hazards, and implementing measures to mitigate or eliminate them.